Importance of Corrosion-Resistant Components in Marine Systems
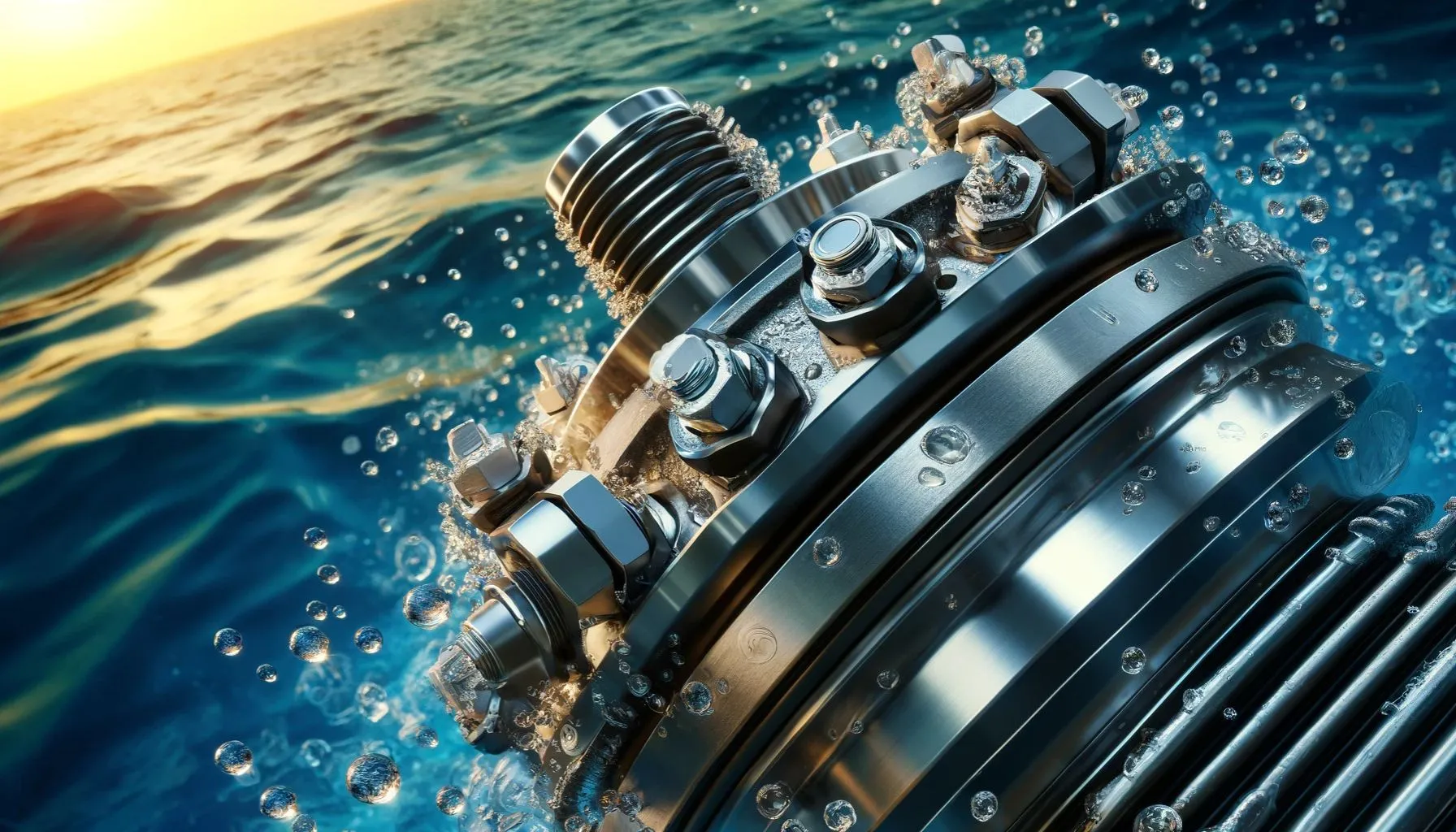
Marine systems operate in some of the harshest environments on Earth. Constant exposure to saltwater, high humidity, and fluctuating temperatures accelerates material degradation, making corrosion-resistant components critical. These materials and technologies ensure longevity, safety, and efficiency while minimizing costs and environmental impact.
Why Corrosion-Resistance Matters in Marine Systems
1. Increased Longevity
- Corrosion-resistant materials, such as stainless steel and advanced polymers, withstand the harsh marine environment, significantly extending the lifespan of boats, ships, and other structures.
- Durable materials reduce wear and tear, limiting the need for frequent replacements.
For more insights on how electronic throttle control enhances marine system efficiency, check out How Electronic Throttle Control Improves Marine Efficiency
2. Enhanced Safety
- Corroded components can fail, leading to dangerous situations such as hull breaches or mechanical breakdowns.
- Corrosion-resistant materials maintain structural integrity, ensuring the safety of crew, passengers, and cargo.
3. Lower Maintenance Costs
- Repairing corrosion-related damage is expensive and time-consuming.
- Components made with corrosion-resistant materials require less frequent maintenance, reducing overall operational expenses.
4. Environmental Protection
- Corroded materials can release harmful substances into the ocean, polluting marine ecosystems.
- Using corrosion-resistant components minimizes material degradation and its environmental impact.
5. Consistent Performance
- Corrosion affects the efficiency of mechanical and electronic systems, leading to failures or reduced functionality.
- Corrosion-resistant components ensure smooth and reliable performance, even under extreme conditions.
6. Adaptability to Harsh Conditions
- Marine environments involve salt spray, constant water contact, and temperature extremes.
- Materials engineered for corrosion resistance excel under these demanding conditions, offering dependable performance.
For more insights on throttle actuator assemblies and their role in electric boats, refer to Throttle Actuator Assembly for an Electric Boat RV4DAYSD602A
Common Applications in Marine Systems
1. Boat Hulls and Structures
- Ships and boats use corrosion-resistant steel, aluminum alloys, or fiberglass to prevent saltwater damage and maintain strength.
2. Propulsion and Control Systems
- Propellers, throttle actuators, and shafts made of corrosion-resistant materials operate efficiently even in submerged environments.
3. Electrical Systems
- Marine-grade wires, connectors, and enclosures resist corrosion, ensuring the reliability of navigation, communication, and power systems.
4. Marine Infrastructure
- Offshore platforms, piers, and docks incorporate corrosion-resistant coatings and materials to endure continuous seawater exposure.
Challenges of Corrosion in Marine Environments
- Accelerated Degradation
- Saltwater acts as an electrolyte, speeding up chemical reactions that cause corrosion.
- Galvanic Corrosion
- Occurs when different metals come into contact in a conductive environment, like seawater.
- Localized Damage
- Pitting and crevice corrosion create small holes or cracks, weakening components.
- Operational Downtime
- Repairs due to corrosion require downtime, disrupting operations and increasing costs.
Materials and Technologies for Corrosion Resistance
1. Stainless Steel
- Contains chromium, which resists rust and staining, making it ideal for marine hardware and structural components.
2. Aluminum Alloys
- Lightweight and corrosion-resistant, commonly used in boat hulls and superstructures.
3. Titanium
- Highly resistant to seawater corrosion but more expensive, used for high-performance marine applications.
4. Protective Coatings
- Coatings like epoxy or polyurethane create a barrier to protect materials from saltwater and humidity.
5. Cathodic Protection
- Uses sacrificial anodes (usually zinc) to prevent corrosion on metal surfaces by redirecting corrosive reactions.
Benefits of Corrosion-Resistant Components
Benefit | Description |
---|---|
Durability | Extends the lifespan of marine systems by resisting wear and tear. |
Cost-Effectiveness | Reduces frequent repairs and material replacements. |
Safety | Prevents critical failures, ensuring reliable operation. |
Eco-Friendly | Minimizes pollution caused by corroded materials. |
Performance Stability | Maintains consistent functionality in harsh environments. |
Future Trends in Corrosion-Resistant Technologies
1. Advanced Materials
- Research is driving the creation of hybrid composites and nanocoatings with superior corrosion resistance.
2. Smart Corrosion Monitoring
- New technologies are integrating sensors into marine systems to detect early signs of corrosion, enabling proactive maintenance.
3. Eco-Friendly Coatings
- Innovations in non-toxic, biodegradable anti-corrosion coatings are becoming a priority to reduce environmental impact.
Conclusion
Corrosion-resistant components are essential for maintaining the reliability, safety, and efficiency of marine systems. By protecting against the harsh conditions of the marine environment, these materials reduce costs, extend lifespans, and support environmental sustainability.
As technology advances, the use of smarter, more eco-friendly corrosion-resistant solutions will continue to improve the performance of marine vessels and infrastructure, ensuring long-term durability and environmental protection.
4 Comments