Steps to Integrate Throttle Actuators into Electric Propulsion Systems
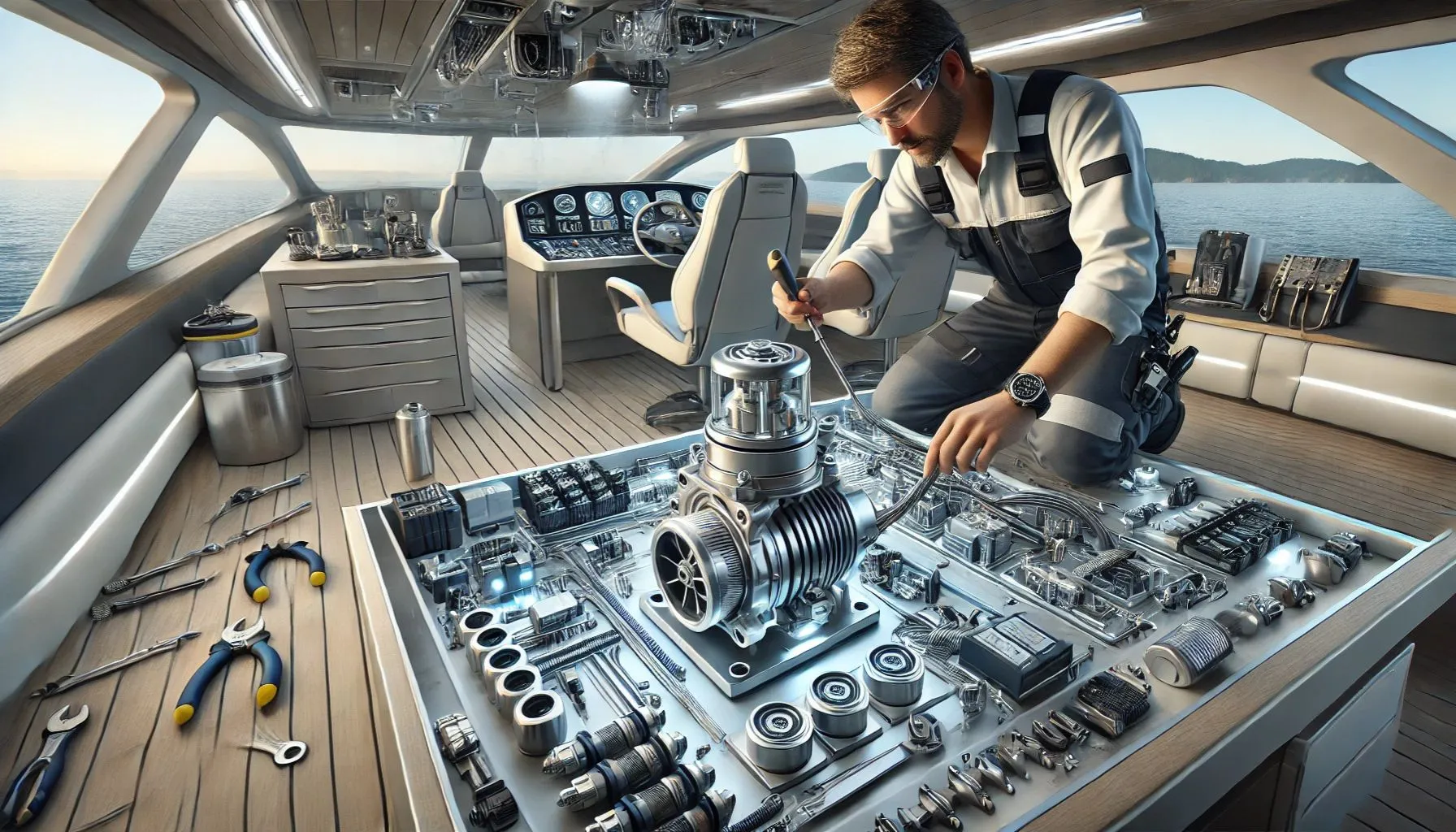
Throttle actuators are essential in electric propulsion systems for managing speed and torque with precision. Integrating them properly ensures optimal performance, energy efficiency, and system reliability. This guide provides a step-by-step process to help you successfully integrate throttle actuators into electric propulsion systems.
Step-by-Step Integration Process
1. System Assessment and Planning
- Evaluate Compatibility: Ensure the throttle actuator matches the electric propulsion motor’s specifications, such as voltage, current ratings, and communication protocols (e.g., CAN bus).
- Plan the Integration: Create a detailed plan, including wiring diagrams, mounting positions, and calibration requirements.
For more insights on throttle actuator assemblies and their role in electric boats, refer to Throttle Actuator Assembly for an Electric Boat RV4DAYSD602A
2. Hardware Selection
- Choose an actuator designed for your system’s environment, especially for marine use where water resistance and corrosion resistance are critical.
- Verify that the actuator complies with safety and industry standards to ensure reliability.
3. Mechanical Mounting
- Position the Actuator: Mount it securely near the propulsion motor, ensuring proper alignment with the throttle mechanism.
- Minimize Vibrations: Use anti-vibration mounts or brackets to protect the actuator from excessive movement.
- Check Linkage: Ensure the actuator linkage moves smoothly with the throttle control arm.
For more insights on how electronic throttle control enhances marine system efficiency, check out How Electronic Throttle Control Improves Marine Efficiency
4. Electrical Connections
- Connect to the Motor Controller: Use shielded cables to reduce electromagnetic interference (EMI).
- Power the Actuator: Use a dedicated circuit that supplies the correct voltage and current.
- Add Sensors: Integrate position or feedback sensors for real-time monitoring of the actuator’s movements.
5. Software Configuration
- Install Compatible Firmware: Ensure the actuator and motor controller use compatible software.
- Set Communication Protocols: Configure CAN bus, Ethernet, or other communication standards to facilitate data exchange.
- Program Parameters: Define throttle range, response time, and fail-safe settings in the actuator’s software.
6. Calibration and Testing
- Synchronize Actuator and Motor: Calibrate the actuator to match the motor’s throttle range and operational settings.
- Test Responsiveness: Run tests under various load conditions to check smooth acceleration and deceleration.
- Verify Output: Use diagnostic tools to ensure the throttle position corresponds accurately to power output.
For more insights on the importance of corrosion-resistant components in marine systems, visit Importance of Corrosion-Resistant Components in Marine Systems
7. Safety and Redundancy Checks
- Implement Fail-Safes: Ensure the actuator can return to a neutral position during faults.
- Backup Systems: Add redundancy features, such as backup power supplies, for consistent operation during failures.
- Test Emergency Functions: Verify the emergency stop system for operator safety.
8. Integration with Control Systems
- Connect to Primary Controls: Link the actuator to the boat’s control panel or joystick for seamless operation.
- Sync with Auxiliary Systems: Integrate with autopilot or dynamic positioning systems for advanced functionalities.
- Enable Real-Time Monitoring: Use onboard diagnostics to track actuator performance.
9. Environmental Testing
- Test in Real Conditions: Operate the system in environments with varying temperatures, humidity, and vibrations to ensure durability.
- Marine-Specific Tests: For marine applications, check corrosion resistance through saltwater exposure tests.
For more insights on common challenges in marine throttle actuator installations, check out Common Challenges in Marine Throttle Actuator Installations
10. Final Deployment and Maintenance Setup
- Conduct a Trial Run: Test the system under normal operating conditions to verify functionality.
- Schedule Maintenance: Establish a routine for inspecting wiring, sensors, and calibration settings to ensure long-term reliability.
Challenges and Solutions
Challenge | Solution |
---|---|
Electrical Interference | Use shielded cables and proper grounding to minimize EMI. |
Calibration Errors | Employ diagnostic tools for accurate calibration and synchronization. |
Environmental Stress | Use corrosion-resistant and sealed components to withstand harsh conditions. |
Software Incompatibility | Update firmware and check compatibility with the motor control system. |
Benefits of Proper Integration
- Improved Efficiency:
- Ensures precise throttle control, optimizing energy use and reducing waste.
- Enhanced Safety:
- Smooth throttle response minimizes operational risks.
- Increased Longevity:
- Reduces wear and tear on the actuator and propulsion motor.
- Better User Experience:
- Provides seamless and intuitive control for operators.
For more insights on the benefits of semi-automated controls in modern electric boats, visit Benefits of Semi-Automated Controls in Modern Electric Boats
Conclusion
Integrating throttle actuators into electric propulsion systems is a multi-step process that requires attention to mechanical, electrical, and software details. By following this guide, you can ensure reliable performance, enhanced safety, and energy efficiency. Proper planning, testing, and maintenance are key to achieving a smooth integration that meets the demands of modern electric propulsion systems.
3 Comments